Building Materials Manufacturer
Staying Competitive with Industrial IoT at Scale
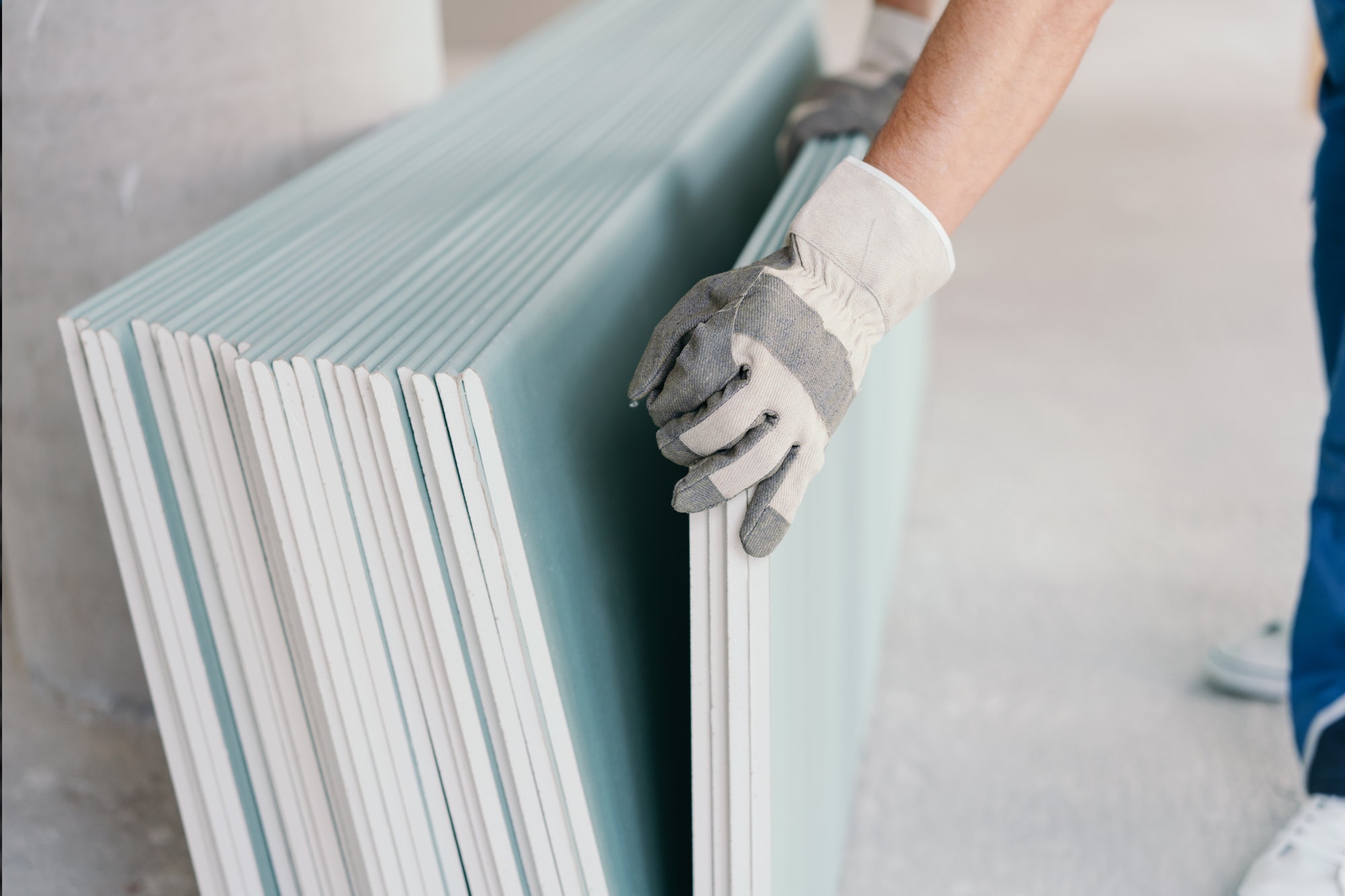
Business overview
This long-established U.S. manufacturing company operates more than 60 plants nationwide and is a top global producer of construction materials like drywall panels, joint compound, and ceiling systems. With a legacy of innovation and plant modernization, they continually seek operational efficiencies to maintain leadership in a competitive market
The challenge
Despite early adoption of Docker and sensor-driven automation, the team struggled to scale containerized workloads across dozens of plants:
- A single Docker expert became a bottleneck, running up to 40 manual deployments per day
- Data scientists lacked CLI skills, slowing iterative model updates
- Command-line deployment was error-prone and unmanageable across growing on-premises infrastructure
- High operational friction risked production quality and uptime during frequent updates
The real-world impact of smarter container management.
Proven at
Scale
Platform
Agnostic
A Collaborative Community
The solution
Portainer transformed the company’s IIoT deployment model:
- Enabled one-click deployment to all edge cameras and sensors across multiple plants
- Eliminated repetitive command-line operations—data scientists now push updates with a few clicks
- Used RBAC to secure an air-gapped environment while delivering consistent configurations
- Centralized container lifecycle management ensured rapid, error-free roll-outs across the entire footprint
"We have had tons of sensors connected to programmable logic controllers (PLCs) for decades. We have essentially used Portainer to turn dumb cameras into a smart IoT device."
"It can take months, or even entire quarters to truly get comfortable with Docker. Some people never reach that point,” says the Linux team lead. “Portainer puts the power of containers into the hands of everyone; technicians and data scientists alike, without the steep learning curve.”
"With Portainer we can update a plant with the push of a button. It's a continuous integration and deployment capability."
“A full line stoppage is hard to put a number on—but we know it would be expensive,” says the team leader. “That’s why we designed this system to isolate issues at the conveyor level. We can absorb smallinterruptions without bringing down the entire line, which helps us avoid the massive costs associated with full production halts.”
(Industry data suggests that large U.S. manufacturers lose an average of $532,000 per hour during line stoppages due to lost revenue, penalties, and restart overhead.)